Technical Skills Training
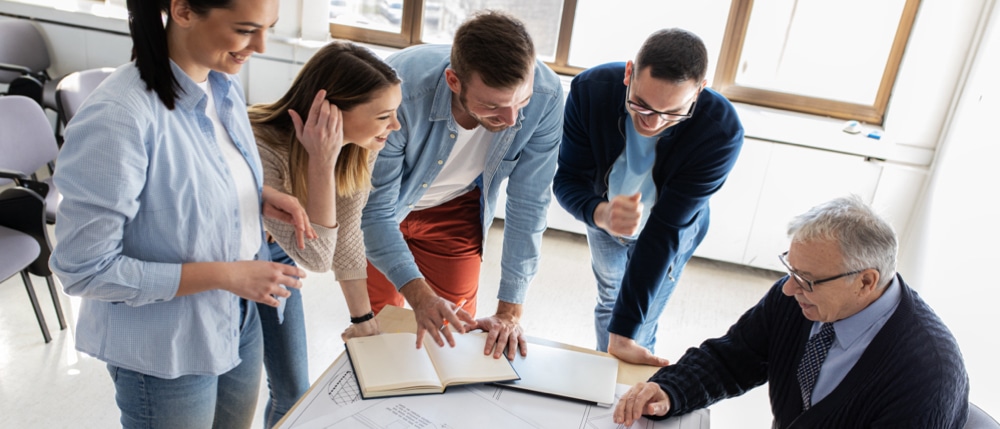
Technical Skills Training
- Do current or projected skill shortages pose a significant challenge to your organization?
- How prepared is your organization to address these challenges?
- What key functions pose the greatest challenge?
- Are individuals responsible for key relationships or operating procedures projected to retire?
- Are your managers and leadership positioned to effectively manage your talent and internal expertise to adequately address these challenges?
Skills gaps impact an organization at all levels – operations, finance, leadership.
Assess the Current Situation
New Hampshire MEP’s Critical Skills Assessment is a facilitated, self assessment that gathers data about your company and the currents skills level and gaps in technical knowledge.
It will provide the data necessary to determine direction and priorities in the following categories:
- Addressing potential skill shortages in key function areas
- Assessing the impact of an aging workforce on your organization
- Evaluating and modifying your training and development programs
- Training recommendations for assessed personnel
- Key performance indicators and the financial impact on your organization
- Recruitment strategies to assist your organization in finding qualified new hires
An in-depth report, including a training matrix, will provide baseline information that can be used to facilitate a discussion on your current strengths and weaknesses in these areas.
Call New Hampshire MEP at 603-226-3200 to schedule an assessment of your current workforce needs.
Recruit & Train the Right People
Approximately 70% of manufacturing skills are basic and universal to all manufacturing occupations.
According to the US Department of Labor, the cost of hiring and then firing an employee whose skill sets do not meet job demands equates to 30% of a year’s salary. Other organizations place the figure between 25 and 200%!!
Critical Occupational REadiness (CORE) Skills Training
An intense, focused practical skills, theory, and hand-on curriculum conducted over two consecutive weeks. The curriculum is instructor lead with self paced computer training modules. The curriculum can be customized to meet a specific need. Each module contains a series of tests to measure each student’s comprehension of the material. The unique “fast track” training process is designed to produce basically trained employees for manufacturing companies. Total Hours: 80.
Intermediate and Advanced Technical Skills Training
Course Offerings Include:
- Geometric Dimensioning & Tolerancing
- Blueprint Reading and Engineering Drawing
- Statistical Process Control
- G&M Programming for Operators
- MasterCam
- Programmable Logic Controllers
- Leadership Training
- Team Involvement Problem Solving
- Effective Communication and Conflict Resolution Workshop
To learn more or schedule training, contact Training Coordinator Jill Duddy at jilliand@nhmep.org.