“Both certifications opened doors we couldn’t access before, especially in the aerospace and defense industries,” said Marcel Labonville, President of Pro Cut CNC Machine, Inc. “We secured a new customer working with a major aerospace firm, and that relationship has helped to re-secure our financial stability.”
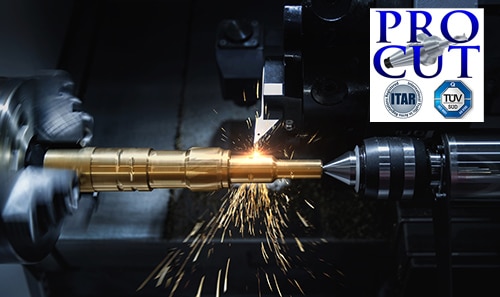