Training Within Industry
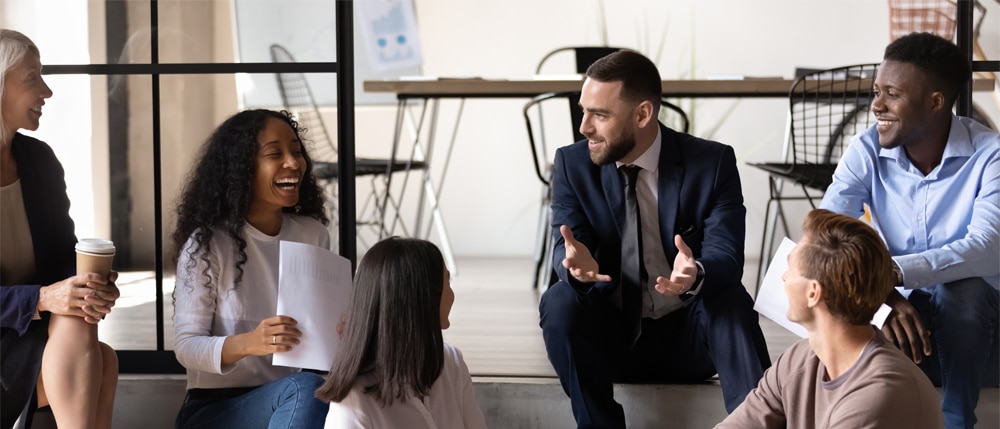
What is TWI?
TWI consists of three standardized programs that teach the essential skills needed by all supervisors and team leaders to create the culture required to lead an organization through a Lean Transformation. These programs are: Job Instruction Training (JI), Job Methods Training (JM), and Job Relations Training (JR).
Job Instruction Training (JI)
Teaches supervisors how to quickly train employees to do the job correctly, safely, and conscientiously. Important steps and key points. The objective is to help supervisors develop a well-trained workforce resulting in less scrap and rework, fewer accidents, and less tool and equipment damage. Supervisors are taught how to effectively break down a job for instruction. The method emphasizes preparing the operator to learn, giving a proper demonstration, identifying the key points in the job, observing the operator perform trial runs, and tapering off coaching while continuing to follow up.
Job Methods Training (JM)
Teaches supervisors how to improve the way jobs are done. The aim of the program is to help produce greater quantities of quality products in less time by making the best use of the people, machines, and materials now available. Supervisors are taught how to break down jobs into their constituent operations. They question details and develop new methods by eliminating, combining, and rearranging these details.
Job Relations Training (JR)
Teaches supervisors how to build positive employee relations, increase cooperation and motivation, and effectively resolve conflicts. JR emphasizes that people must be treated as individuals. Supervisors are given foundations for developing and maintaining good relations to prevent problems from arising. Principles include providing constructive feedback, giving credit when due, telling people in advance about changes that will affect them, making the best use of each person’s ability and earning the employee’s loyalty and cooperation. When problems do arise, it teaches supervisors how to get the facts, weigh them, make the decision, take action, and check results.
Participants attend class for 2 hours each day for 5 consecutive days and they return to the workplace after each session to apply the techniques learned. Each participant must select a current day workplace problem and demonstrate to the class how they applied the method to solve that problem. Class materials include pocket reference cards for daily use to keep the improvements coming after the training has been completed. Small class sizes of from 8 to 10 people keep everyone involved to maximize learning.
All TWI programs follow the proven four-step methodology of Preparation, Presentation, Application and Testing that makes each program simple, straight-forward and easy to implement. Supervisors are given the opportunity to practice the four-step method and “learn by doing” in a confidential, low-stress, and highly supportive environment. TWI takes you to the next step in the Lean journey.
TWI History
Training within Industry (TWI) was one of the first emergency services established for training during WWII (early 1940’s). Its purpose is to rapidly train inexperienced supervisors and workers to improve productivity within a manufacturing company.
TWI training results in each worker making full use of his/her best skill; maximizing their individual ability and contribution to the organization. It establishes Train the Trainers within your company who can train others by using a “learn by doing:” model. The knowledge stays within the company and does not leave when an employee leaves.
Over 600 client companies attributed the following results to TWI (1940’s):
• 86% increased production by at least 30%
• 100% reduced training time by 28% or more
• 88% reduced labor-hours by over 25%
• 55% reduced scrap by at least 25%; • 100% reduced grievances by more than 30%
TWI Institute Web Site Link
For more information or to schedule a TWI program for your team, contact Training Coordinator Jill Duddy at (603) 226-3200 or jilliand@nhmep.org.