Project Management
Project Management and Agile Workshop Courses
New Hampshire MEP is now providing manufacturers with two new exciting offerings – a 2-day Intro to Project Management course and a 3-day Introduction to Agile workshop. These courses are conveniently booked by appointment to work with your team’s busy schedule.
Introduction to Project Management
Workshop Overview
This program is designed for participants who are new to project management and those requiring a refresher. The two-day program is organized in 5 modules. Each module can be extended or reduced depending on the specific learning needs of the participants. This course is presented in a highly interactive style with plenty of practical exercises, break-out group work and discussion. Participants work in teams on actual projects that they bring to the course.
Learning Objective
- Define and use project management principles
- Apply appropriate tools and techniques to meet project management challenges
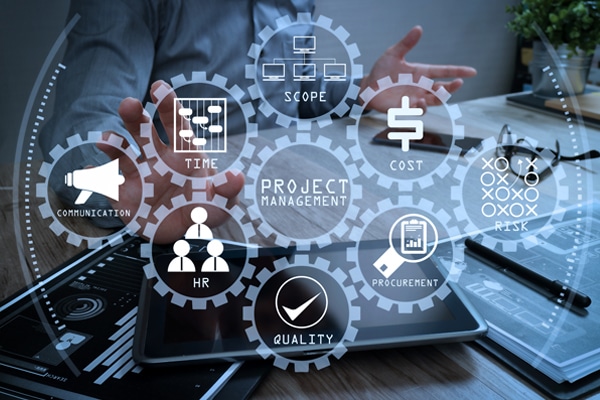
COURSE OUTLINE – DAY 1
MODULE 1 // Introduction to Projects
Attendees identify characteristics of projects.
• Course Overview
• Definition of a project
• Aspects of project success
• Waterfall and Agile compared
MODULE 2 // Project Initiation
Working in teams, attendees develop Project Charters for their projects.
• Business strategy
• Stakeholders
• Project scope and priorities
• The Vision
EVENT DETAILS
LOCATION: In-person class OR each module can be presented as a 3-hour webinar
COURSE LENGTH: 2 Days
TIME: 09:00 AM – 4:00 PM
DATE: Courses are reserved by appointment. Contact us to schedule a date.
COURSE OUTLINE – DAY 2
MODULE 3 // Project Planning
Attendees learn to write a practical project plan.
• Work Breakdown Structure
• Communication Plan
• Staffing Plan
• Risk Management
• Quality
• Estimation and Scheduling
MODULE 4 // Executing, Monitoring and Controlling the Project
Attendees learn tools and techniques for effectiveness during project execution.
• Information Management
• Effective Meetings
• Procurement Management
MODULE 5 // Closing the Project
Attendees learn methods for capturing lessons learned for application on future projects.
• Retrospectives
• Acceptance of Deliverables
• Course Summary
For more information or to schedule a course, please call Jill Duddy at (603) 226-3200 or jilliand@nhmep.org.
Introduction to Agile Workshop
Workshop Overview
This program is designed for participants who are new to Agile project management and those requiring a refresher.
The three-day program is organized in 6 modules. Each module can be extended or reduced depending on the specific learning needs of the participant.
This course is presented in a highly interactive style with plenty of practical exercises, break-out group work and discussion. Participants work in teams on actual projects that they bring to the course.
Learning Objective
- Define and use Agile project management principles
- Apply appropriate tools and techniques to meet project management challenges
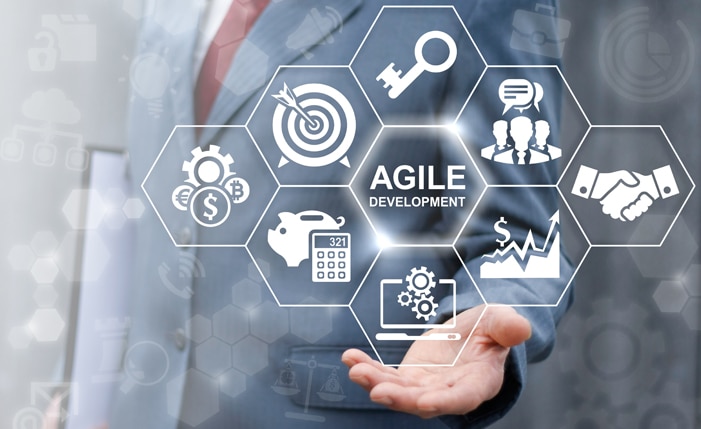
COURSE OUTLINE – DAY 1
MODULE 1 // Understanding projects and the Scrum framework
Attendees identify characteristics of projects and learn the processes of the Scrum methodology as an example of Agile project management.
• Definition of a project
• Aspects of project success
• Waterfall and Agile compared
• The Agile Manifesto
• Agile Teams
• Scrum Overview
MODULE 2 // Aligning projects with the needs of the business
Projects exist to deliver business value: from financial results to specific organizational needs. In this module, attendees develop Agile Charters.
• Business strategy
• Stakeholders
• Project scope and priorities
• The Vision
EVENT DETAILS
LOCATION: In-person class OR each module can be presented as a 3-hour webinar
COURSE LENGTH: 2 Days
TIME: 09:00 AM – 4:00 PM
DATE: Courses are reserved by appointment. Contact us to schedule a date.
COURSE OUTLINE – DAY 2
MODULE 3 // Managing the Product Backlog
Attendees learn how to write good User Stories in order to understand customer requirements.
• User Roles
• The User Story Template
• Just-In-Time Requirements
• Splitting User Stories
• Acceptance Criteria
• Sprint Planning
MODULE 4 // Sprint Execution
The bulk of each sprint is spent in execution – getting things done. Attendees learn techniques for completing work and tracking progress.
• Agile Estimation
• Risk Identification
• Definition of Done
• Daily Scrum
• Task Boards
COURSE OUTLINE – DAY 3
MODULE 5 // Inspect and Adapt
The end of each Sprint is dedicated to collecting feedback and insight into how best to approach the next Sprint.
• Working with customers
• Sprint Demo
• Sprint Retrospective
• Agile over Time
MODULE 6 // Special Topics
Attendees prioritize topics based on needs and interest. Options include:
• Agile Contracts and Procurement
• Kanban
• Information Radiators