Lean Product Development
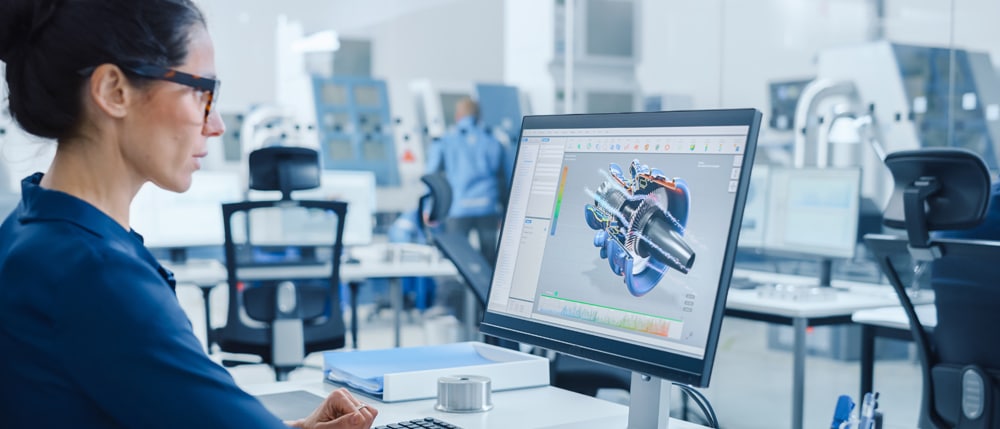
Lean Product Development “Quickstart” 2 Day Workshop
This workshop is designed to introduce executive managers, department heads and employees in marketing, engineering, finance and administration – to the benefits and methodologies of Lean Product Development. The six workshop segments include the five “events” of the ideal “Quickstart” lean product development process along with a segment devoted to management systems and methods that are the “glue” that holds the process together. Hands-on exercises by interdisciplinary client “teams” demonstrate the tools and the integrated product team approach inherent in LPD
Main Workshop Segments:
Overview and Workflow Management System Methods
Introduces a simplified project management workflow system and methods. These enable dramatic reductions in time-to-market while increasing development resource capacity. The objective of this section is to equip participants with lean product development management tools (such as visual boards and stand-up meetings); development principles; techniques; and best practices that can be deployed immediately to enable rapid, high-value project development.
Market Requirements Event Participants are shown how customer needs and/or requirements can be converted through systematic tools, into prioritized engineering specifications. The primary inputs to the event are voice-of-the-customer data, market requirements brief, and competitive data; and the key outputs are a prioritized list of high-level engineering requirements, a market positioning statement and a set of action items to be executed during the concept design activity.
Planning/Risk Management Event
Participants are shown realistic project planning methods, including schedule, launch date, budget, and a resource plan, and how to perform proactive risk identification and mitigation for the project. Project prioritization strategies are also discussed. The key outputs of this event include the project budget and resource plan, the project milestone schedule, a prioritized list of risk issues, and action assignments for risk mitigation.
3P/Cost Reduction Event (Design 3P)
Participants are shown innovative cost reduction and quality enhancement tools to reduce product manufacturing cost and improve manufacturability and delivered quality – before significant project costs are incurred. Key outputs of this event include a preliminary manufacturing plan, prioritized lists of critical-to-quality and critical-to-cost improvements, capital plan, and action items to implement.
Design Review and Freeze Event
Participants are shown how this event reviews and finalizes specifications, timelines and costs, and generates prioritized lists of corrections, improvements and a master action list as outputs in preparation for production launch.
Production Readiness Review Event
Participants are shown how this event verifies and finalizes that all critical actions from the Master Action List have been completed, including qualification test data, final production launch plan, final layout for lines and cells, poke-yoke/fixturing/equipment, test/inspection, sourcing/supply chain, distribution/logistics, and sustaining support.
For more information contact Zenagui Brahim at (603) 226-3200 or zenaguib@nhmep.org